Kupfer
Kupfer gehört zu den ältesten Werkstoffen der Erde. Schon früh erkannten die Menschen, dass sich durch das geschickte Mischen von verschiedenen Metallen, Legierungen herstellen lassen, die dann verbesserte Eigenschaften als die jeweiligen Ausgangsmaterialien aufweisen. In Palästina entstanden, bereits um ca. 1400 v. Chr., die ersten Kupfer-Zink-Legierungen, indem Zinkkarbonat beim Schmelzen von Kupfer hinzugefügt wurde.
So liegt der Ursprung von Messing über 3000 Jahre zurück.
Um 150 n. Chr. wurde nach dem gleichen Verfahren auch auf deutschem Boden Kupfer-Zink-Legierungen hergestellt. Die industrielle Herstellung dieser Legierung läßt sich in Deutschland bis in das 15. und 16. Jahrhundert zurückverfolgen.
Matthies Druckguss verarbeitet bereits seit der Firmengründung 1955, die im Druckguss am besten geeignetsten Kupfer-Zink-Legierungen. Wir sind damit der älteste Messing-Druckgiesser in Deutschland!
Einteilung der Kupfer-Zink-Legierungen
Messing wird eine Gruppe an Legierungen genannt, die auf der Basis aus Kupfer mit Zink als Hauptlegierungselement besteht. Im Druckguss haben sich zwei Hauptgruppen an Legierungen durchgesetzt, sogenannte Messing- und Sondermessinglegierungen.
Durch das Legieren mit weiteren Elementen wie z.B. Zinn, Aluminium, Blei, Nickel oder Chrom, einzeln oder kombinierend, lassen sich hervorragende mechanische und/oder chemische Eigenschaften erreichen. Das Ergebnis können Legierungen sein, die hohe Festigkeitswerte, eine guten Zerspanbarkeit oder eine sehr gute Beständigkeit gegen Korrosion aufweisen.
Im Druckguss haben sich zwei Messinglegierungen in der Norm DIN 1982 etabliert: die Messinglegierung CuZn39Pb1Al-C-GP und die Sondermessing- oder Tombaklegierung CuZn16Si4-C-GP, auch bekannt unter den Bezeichnungen Olkusil bzw. Tombasil. Diese Begrifflichkeiten finden jedoch nur noch im englischsprachigen Raum Anwendung. In Tabelle 5 ist die chemische Zusammensetzung der Messinglegierung CuZn39Pb1Al-C-GP aufgeführt.

Tabelle 5
Der relativ hohe Bleigehalt von 0,5 bis 2,5 % verbessert entscheidend die Zerspanbarkeit, eine Überschreitung der oberen Toleranz steigert jedoch die Warmbrüchigkeit, so dass ein sicheres Entformen nicht mehr gegeben ist. Durch den Zusatz von bis zu 0,8 % Aluminium wird die Zinkoxidation bzw. –verdampfung der Schmelze beim Warmhalten im Tiegelofen sowie beim Schöpfen und Dosieren verringert. Das zugegebene Nickel steigert im Zusammenspiel mit Mangan die Korrosionsbeständigkeit. Neben der guten Zerspanbarkeit weist diese Legierung eine gute Korrosionsbeständigkeit gegen Trink- und Brauchwasser auf. Die mechanischen Eigenschaften sind in Tabelle 6 aufgeführt.

Tabelle 6
Der Kupfergehalt der Tombaklegierung ist mit einem Wert im Bereich von 78,0 – 83,0 Massenprozent zwischen 15 % und 20 % höher als bei der Messinglegierung. Der dadurch geringer ausfallende Zinkgehalt von unter 20 % steigert die Entzinkungsbeständigkeit und führt zusammen mit den Legierungselementen Aluminium, Nickel und Zinn zu einer erheblichen Verbesserung der Korrosionsbeständigkeit bis hin zur Salzwasserbeständigkeit. Ein Bleianteil von bis zu 0,8 % dient auch hier zur Erleichterung der Zerspanbarkeit. Diese Legierung lässt sich jedoch nur mit Hartmetall-Werkzeugen bearbeiten. Der relativ hohe Anteil an Silizium im Bereich von 3,0 – 5,0 % steigert, neben der Dünnflüssigkeit, die Zugfestigkeit auf einen Wert von bis zu 500 N/mm², bei gleichzeitiger Senkung des Schmelzpunktes.
Der starke Einfluss des Legierungselements Silizium führte zur Namensausprägung Silizium-Tombak (Tombak vom malaysischen Namen für Kupfer „Tambaga“).
Zustandsschaubilder
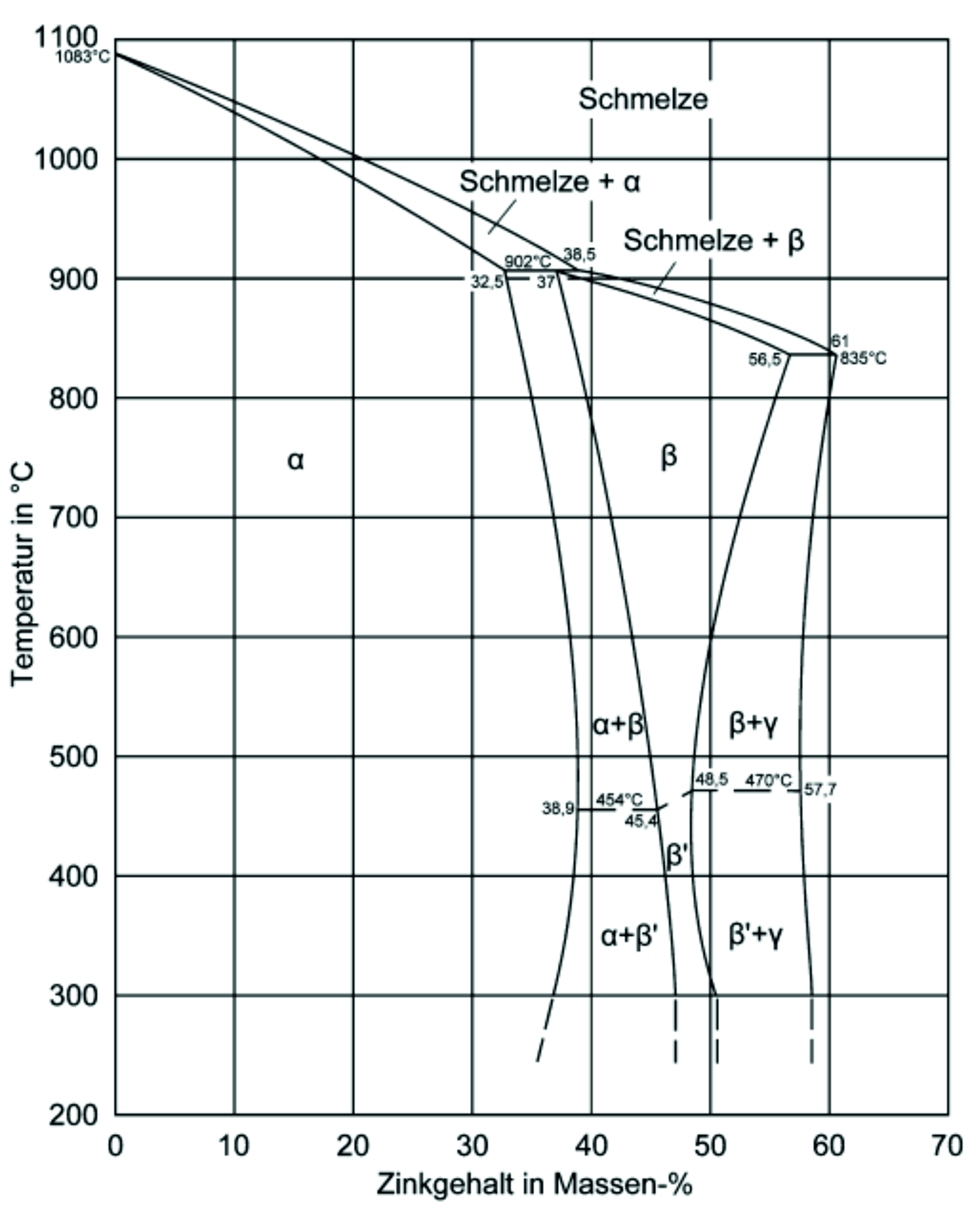
Dieses Bild zeigt das Zustandsschaubild der Kupfer-Zink-Legierungen, dargestellt im technisch wichtigen Konzentrationsbereich von 0 bis 60 % Zink.
Aufgrund ihres Gefügeaufbaus können Kupfer-Zink-Legierungen in drei Hauptgruppen unterteilt werden:
- Bis ca. 37% Zink weisen einheitliches Gefüge auf (α-Phase) und kristalliert kfz
- 37-46% Zink (ß-Phase) erstarrt kubisch-raumzentriert (krz), zusätzlich α+ß Gefüge mit geringerer Plastizität, Anteil am Gesamtgefüge steigt mit dem Zinkgehalt
- 46-50% Zink einheitliches Gefüge (ß-Phase)
Bei höheren Zinkgehalten tritt die γ-Phase als weiterer Gefügebestandteil auf, durch die extreme Sprödigkeit werden solche Legierungen allerdings technisch unbrauchbar
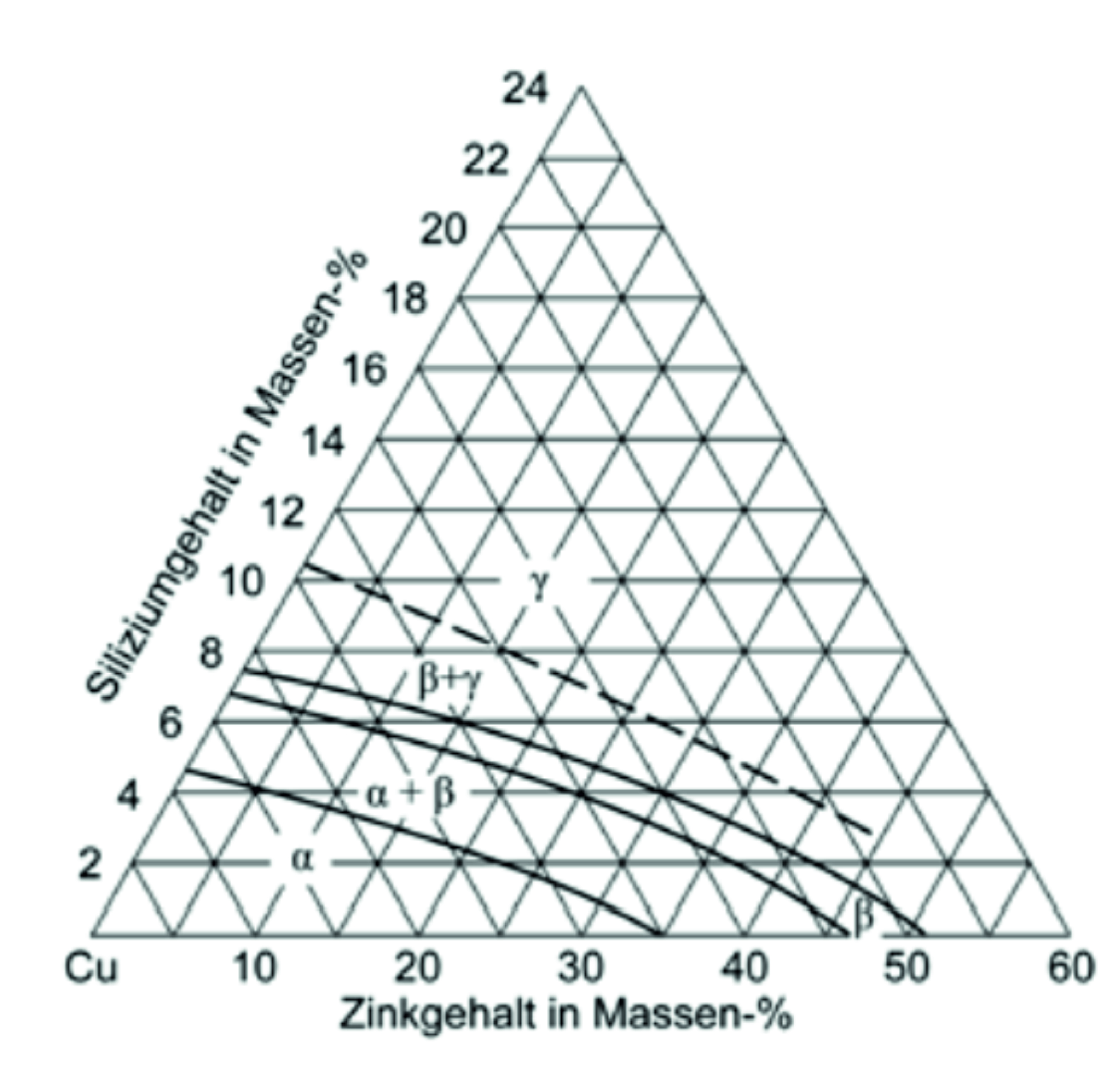
Dieses Bild zeigt das Zustandsschaubild der Kupfer-Zink-Silizium-Legierungen, dargestellt im technisch wichtigen Konzentrationsbereich von 0 bis 60 % Zink.
Etwa 4 % Silizium sind im Kupfer lösbar, jedoch nimmt die Löslichkeit mit zunehmenden Zinkgehalt ab, in einphasigen (α)-Kupfer-Zink-Legierungen mit 68 % Kupfer sogar bis auf 0,5 % Silizium.
In zweiphasigen (α+β) Kupfer-Zink-Legierungen verbessert Silizium die mechanischen Eigenschaften. Wenn Silizium in gleichmäßiger Lösung vom Mischkristall aufgenommen wird, vermindert es die Empfindlichkeit der Spannungsrisskorrosion und zudem der Zinkausdampfung bei der Wärmebehandlung. Zudem verbessert es die Gießbarkeit erheblich.