Allgemein
Betrachtet man die Temperaturdifferenz des Gießzyklusses, also unmittelbar nach Öffnen der Form, über das Auswerfen des Gussteils, das Sprühen der Kavitäten und das Schließen der Form bis zum folgenden Füllen der Form mit flüssigem Metall, so lässt sich bei Messinglegierungen etwa eine Temperaturdifferenz ∆T zwischen 500 bis 600 °K messen. Die Formgravur mit allen dazugehörigen Bestandteilen, wie z. B. eingesetzten Kernen, vorstehenden Stegen und/oder scharfkantigen Übergängen, ist somit sehr starken thermischen Belastungen ausgesetzt. Bei diesem ∆T befindet sich der Warmarbeitsstahl permanent von Zyklus zu Zyklus im Stresszustand zwischen der fast erreichten Anlasstemperatur beim Formfüllen und der anschließenden Abschrecktemperatur nach dem Ausstoßen des Gussteils und dem Sprühen der Kavitäten.
Die Druckgussformen sind daher aus sehr speziellen Warmarbeitsstählen hergestellt, damit die Formen während des Prozesses äußerst stabil sind und den extremen thermischen Beanspruchungen während der Produktion standhalten können.
Um die Standzeit der Formen nicht unnötig zu senken, sollte die Gussteilkonstruktion im Vorwege so optimiert werden, dass möglichst kaum oder gar keine Stressbelastung von der Kavität (Bauteilgeometrie an sich) ausgeht. Mit den folgenden Hinweisen erhalten Sie eine Hilfestellung zur optimalen Gestaltung sowie allgemeine Tipps für eine einfache und eindeutige Kommunikation der technischen Anforderungen an das Gussteil
Bemaßung
Die Zeichnung sollte grundsätzlich so bemaßt werden, daß neben den Nennmaßen auch die geforderten Besonderheiten im Druckguss gewürdigt werden. Hierzu gehört insbesondere die Angabe der Oberflächenrauheit sowie Angaben zur Oberflächenbeschaffenheit (Rohguss oder nachträglich bearbeitet). Mit Ausnahme der Bemaßung der Wanddicke ist eine Kettenbemaßung zu vermeiden.
Radien
Allgemein sollten Druckgussteile keine „scharfen Kanten“ (harter Kantenbruch) aufweisen, da dieser beim Gießen zu Problemen führt.
Äußere Kantenübergänge sollten mit mindestens R 1-2 mm verrundet ausgeführt werden, um ein sicheres Entformen und damit ein sauberes Gussteil zu ermöglichen. Kleinere oder gar keine Radien führen zur Rissbildung im Gussteil und zu einer erfrühten Rissanfälligkeit in den Oberflächen der Kavität.
Innere Kantenübergänge sollten ebenfalls nicht scharfkantig ausgeführt werden. Auch hier empfiehlt sich ein Radius zwischen 1-2 mm, je nach genauer Anforderung an das Gussteil. Sofern kein Radius erwünscht ist oder störend sein sollte, können diese natürlich durch eine nachträgliche mechanische Bearbeitung egalisiert werden.
Zu große Radien sind allerdings auch von Nachteil, da sich die Materialanhäufungen in diesem Bereich erhöhen und dann zu erhöhter Lunkerbildung führen können.
Wandstärken und Schwindmaß
Aufgrund der erhöhten Warmbrüchigkeit von Messinglegierungen im Druckguss müssen die Mindestwandstärken von Gussteilen zwischen 2 – 3 mm als absolutes Minimum angenommen werden.
„Dicke Bereiche“, also Bereiche großer Wanddicken (Materialanhäufungen) sollten aufgrund der vermehrten Bildung von Porositäten stets vermieden werden. Zudem kann die Form in diesen Bereichen schneller überhitzen, was zu übermäßigen Verschleiß durch Auswaschungen oder vorzeitige Brandrisse führt.
Aber auch zu geringe Wanddicken führen zu Problemen. Neben der möglichen Unebenheit des Gussteils besteht vor allen Dingen die Gefahr von nicht ausgelaufenen Bereichen (u.a. Kaltfluss). Aber auch das Durchdrücken von Konturen wie z.B. Auswerfern oder Einfallstellen auf der Gussteiloberfläche können die Folge sein.
Senkrechte oder grade Außenkonturen sind zu vermeiden. Hierbei spielt die richtige Wahl der Entformungsschrägen eine Rolle. Da Messinglegierungen ein Schwindmaß von 1,8 – 2,3 % aufweisen, sollten die Aushebeschrägen mindesten 1,5°, besser jedoch 2° pro Seite betragen. Andernfalls wäre ein sicheres Entformen des Gussstücks nicht mehr gewährleistet.
Durch das Schwindmaß werden sämtliche Gussteilmaße beeinflusst. Als einhaltbare Toleranzen für alle nicht mechanisch bearbeiteten Bereiche gelten nach DIN 1687, Teil 4 die Genauigkeitsbereiche GTA13/5, GTA 14, GTA 14/5 und GTA 15 (siehe untenstehende Tabelle 1).
Raumdiagonale und Freimaßtoleranzen
Zur Ermittlung der genauen Toleranz eines bestimmten Nennmaßes nach obiger Tabelle 1, wird wie folgt vorgegangen:
1. Bildung eines prismatischen Hüllkörpers, der um das beliebig geformte Gussteil gelegt wird.
2. Ermittlung der Raumdiagonale durch die Formel: R = √ (L² + B² + H²)
3. In Tabelle 1 unter R die passende Zeile anhand des Ergebnisses auswählen
4. Entscheiden, ob Maß „formgebunden“ (im gleichen Formenteil und/oder durch Formkontur an Schwindung gehindert) oder „nicht formgebunden“ (Lage in verschiedenen Formenteilen und/oder Bereich kann frei schwinden)
5. Nennmaß-Spalte auswählen und Toleranz ablesen
Abbildung 1: Bestimmung der Raumdiagonale
Entformungsschrägen
Da beim Druckguss eine rasche Erstarrung des flüssigen Metalls einsetzt, die eine umgehend einsetzende Schrumpfung des entstehenden Druckgussteils in der Form zur Folge hat, ist es erforderlich, Entformungsschrägen an aufzuschrumpfenden Flächen anzubringen.
Die zu wählenden Werte unterscheiden sich nach Wahl des Druckgießwerkstoffes, der Stückgröße sowie der Lage von möglichen aufschrumpfenden Bereichen. Um Verformungen beim Auswerfen (Ausstossen) des Gussteils zu vermeiden, sollten im Bauteil entsprechende Stütz- oder Verstärkungsflächen angebracht werden, die den Ausstosskräften entgegenwirken. Besonders heikel sind Bereiche, in denen Bohrungen oder andere Vertiefungen, wie auch kleine Taschen, mit Hilfe von Kernen hergestellt werden. Hier sollten die Aushebeschrägen je nach Art des Kerns: a. fester Kern in der Kontur einer Kavität oder b. beweglicher Kern ausgeführt durch einen Schieber (meist quer zur Trennebene) unterschiedlich groß gewählt werden (vgl. Tabelle 2).
Es gibt verschiedene Methoden die Formschräge anzugeben, je nachdem welches Maß am Bauteil als kritisch anzusehen ist. Etabliert haben sich folgende Bezeichnungen:
Kleinstmaß (KM): Formschräge wird dem Nennmaß hinzugefügt
Größtmaß (GM): Formschräge wird vom Nennmaß abgezogen
Mittelmaß (MM): Nennmaß befindet sich genau in der Mitte, +/- Formschräge/2
Allgemein sollte auf der Zeichnung festgelegt werden, ob die Formschräge hinzugefügt (KM), abgezogen (GM) oder gemittelt (MM) werden muß.
Bohrungen und Durchbrüche
Das Vor- und Fertiggießen von Bohrungen ist nur einer der prägenden Vorteile des Druckgießens. Hierbei ist zu beachten, dass durchgehende Kerne günstiger sind als Sacklochkerne. Zudem kommt es auf die Geometrie des herzustellenden Loches an. Wegen der auftretenden Schrumpfkäfte ist das Verhältnis von Durchmesser zu Länge hier der entscheidende Haltbarkeitsfaktor.
Gewinde und Verzahnungen
Innengewinde können nur in Ausnahmefällen und mit erheblichen Aufwand vorgegossen werden. Daher sollten sie im Druckguss vermieden und später in der mechanischen Bearbeitung hergestellt werden. Es ist jedoch möglich die entsprechenden Kernlochbohrungen für die jeweiligen Gewinde bereits komplett vorzugießen.
Außengewinde lassen sich relativ leicht herstellen. Die Gewindeachse sollte mit der Trennebene übereinstimmen. In diesem Bereichen flacht man das Gewinde idealerweise etwas ab, so dass ein gutes Entformen und einfaches entgraten der abgeflachten Fläche möglich ist.
Rippen und Stege
Prinzipiell ist die Gussteilkonstruktion so auszuführen, das Materialanhäufungen (wie oben erwähnt) vermieden werden. Derartige Bereiche sollten „abgespeckt“ werden. Ist in diesen Bereichen eine erhöhte Steifigkeit verlangt, so können Verippungen angebracht werden. Soll z.B. ein Bohrungsdom gegen Verbiegen gesichert werden, so können Rippen in alle vier Richtung abgehend von der äußeren Domwandung, senkrecht zueinander, angebracht werden (wie eine Art Fadenkreuz). Diese können, seitlich betrachtet, entweder als Rechtecke, beginnend vom oberen Punkt des Doms bis zum Grund verlaufen oder vom Grund bis 2/3 Höhe des Doms als Dreiecke ausgeführt werden. Die Wandstärke von Rippen sollte im Allgemeinen mindestens der des Gussteils in diesem Bereich entsprechen und kann bis zu 20% dicker ausgeführt werden.
Hinterschnitte
Hinterschnitte sind Bereiche in der Kontur, die eine entgegengesetzte Entformungsschräge aufweisen oder Schattenbereiche, die hinter der Hauptkontur liegen und somit ein Entformen des Gussteils verhindern würden. Wenn derartige Bereiche nicht durch Kernzugschieber hergestellt werden können, sind sie natürlich zu vermeiden, da sonst eventuell die Herstellung des Gussteils nicht möglich ist. Sofern diese Bereiche konstruktiv gefordert sind, sollte die Herstellung durch mechanische Bearbeitung erfolgen.

Abbildung 2: Hinterschnitte oder Schattenbereiche (links)
Bearbeitungszugaben
Bereiche, die im reinen Gusszustand den geforderten Genauigkeiten nicht genügen (z.B. Dichtflächen, Form- und/oder Lagetoleranzen), müssen mit Bearbeitungszugaben (BEZ) versehen werden, die durch eine nachfolgende mechanische Bearbeitung entfernt werden, um die erforderliche Maßgenauigkeit zu erreichen. Für Kupferlegierungen im Druckguss werden nach Tabelle 4 die Toleranzfelder B bis D angenommen. Weitere Informationen sind in der DIN EN ISO 8062 Teil 3 (2008-09) enthalten.
Versatz
Unter Versatz versteht man die relative Verlagerung von Gußstückflächen infolge von normalen Abweichungen über die Teilungsebene der Formhälften hinweg. Soweit nicht anders vereinbart, muß die Toleranz für den Versatz innerhalb der unter Bearbeitungszugaben (BEZ) genannten Werte angenommen werden.
Eingießteile
Ein großer Vorteil beim Druckgiessen liegt in der Möglichkeit der Nutzung von Eingießteilen. Diese können aus den Materialien Stahl, Kupfer o.ä. bestehen. Sie werden für Bereiche verwendet, die z.B. die Festigkeit des reinen Druckgussteils übersteigen (Lagerbuchsen, Stehbolzen, Gleit- oder Reibflächen).
Es gilt beim Einsatz von Eingießteilen folgendes zu beachten:
- Die Eingießteile müssen für den richtigen Halt in der Formaufnahme, richtig toleriert sein
- Das flüssige Metall muss auf das Eingießteile aufschrumpfen können
- Die Eingießteile müssen eine entsprechende sichernde Oberfläche aufweisen, die ein Verdrehen oder Herausziehen während des Ausstossens oder danach verhindert.
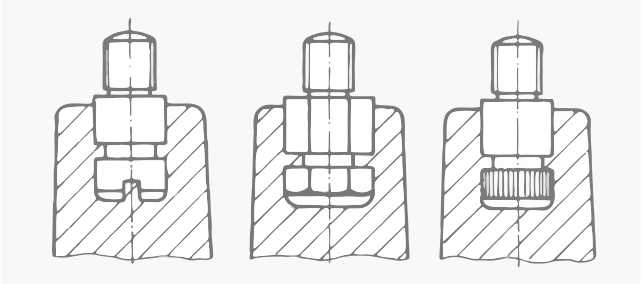
Abbildung 3: Beispiele für die Ausführung der Aufnahme von Eingießteilen
Schriftzeichen
Ohne große Mühen können Schriftzeichen, Nummern oder andere Bezeichnungen auf den Außen- und teilweise auch den Innenflächen fertig mitgegossen werden.
Idealerweise sollte hierfür ein vertiefter Bereich (fliederfarben in der Skizze) mit erhabenen Zeichen (dunkelblau in der Skizze) gewählt werden um auch bei fortschreitenden Formverschleiß eine genaue Kennzeichnung zu ermöglichen. Die erhabene Schrift sollte hierbei in einer Ebene mit der umliegenden Flächenkontur liegen. Nur vorstehende oder zurückstehende Zeichen sind zu vermeiden.
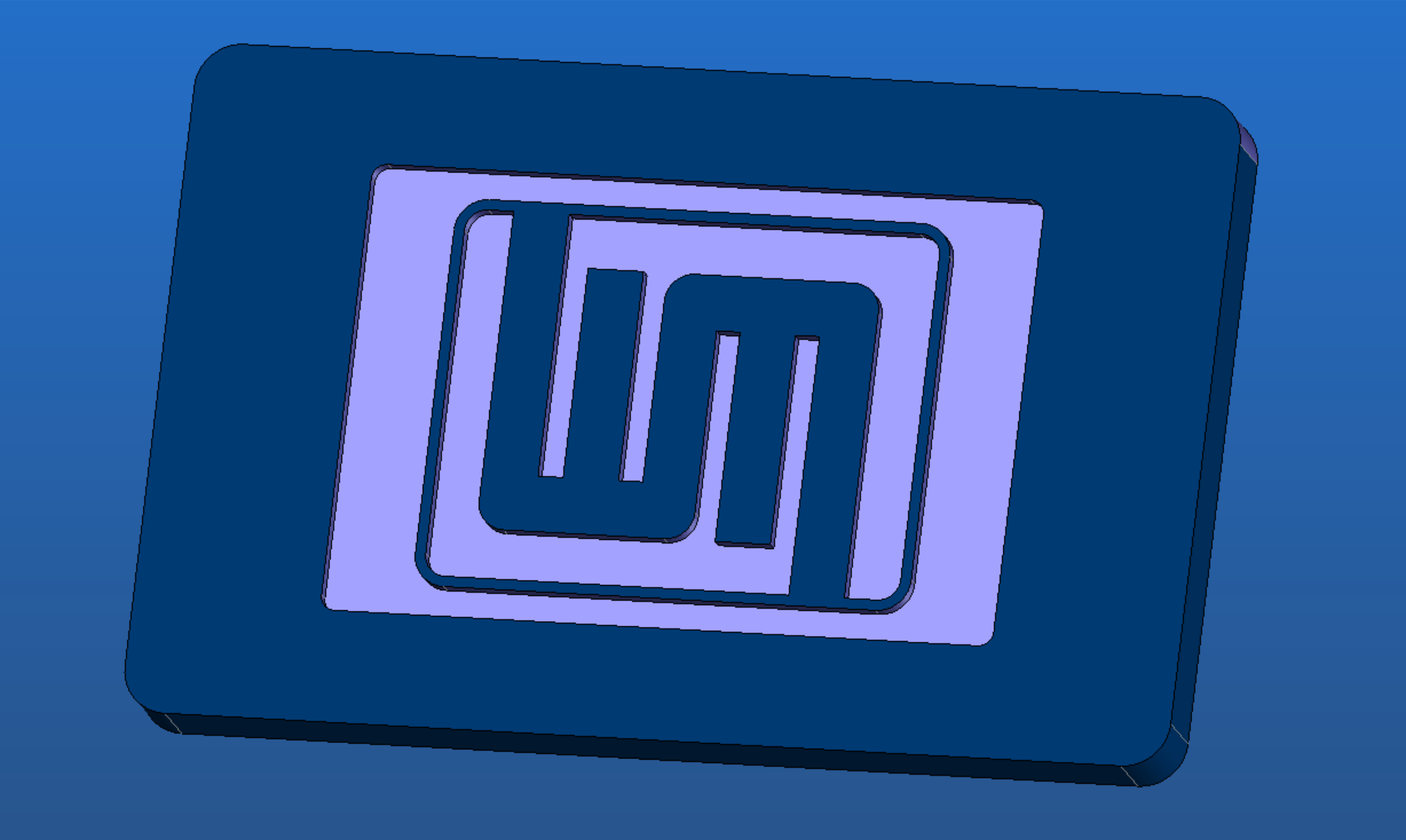
Abbildung 4: Schriftzeichen im Druckguss
Wärmebehandlung von Druckguss
Wenn Druckgussteile nicht gerade im Vakuumdruckgussverfahren hergestellt werden (der Formhohlraum wird vor dem „Schuss“ von Luft evakuiert), so sind sie allgemein nicht wärmebehandelbar.