Gerade bei Messing herrscht meist Verwunderung über die Eignung im Druckgießprozess, ausgelöst durch die besonders hohe Schmelz- bzw. Gießtemperatur. Dabei darf nicht in Vergessenheit geraten, dass Kupfer bzw. Messing einer der ältesten verwendeten Werkstoffe in der Geschichte des Menschen ist.
Druckguss wird all zu häufig als Synonym für ein Gießverfahren genannt, welches als Einsatzmaterial (Legierung) Aluminium oder Zink verwendet. Dagegen ist auch prinzipiell nichts einzuwenden, außer das diese Aussage leider unvollständig ist. Denn auch Messinglegierungen haben einen hohen Stellenwert im Druckguss.
Scrollen Sie weiter runter und erfahren Sie auf den nächsten Seiten selbst, welche Eigenschaften Messing im Druckguss besitzt.
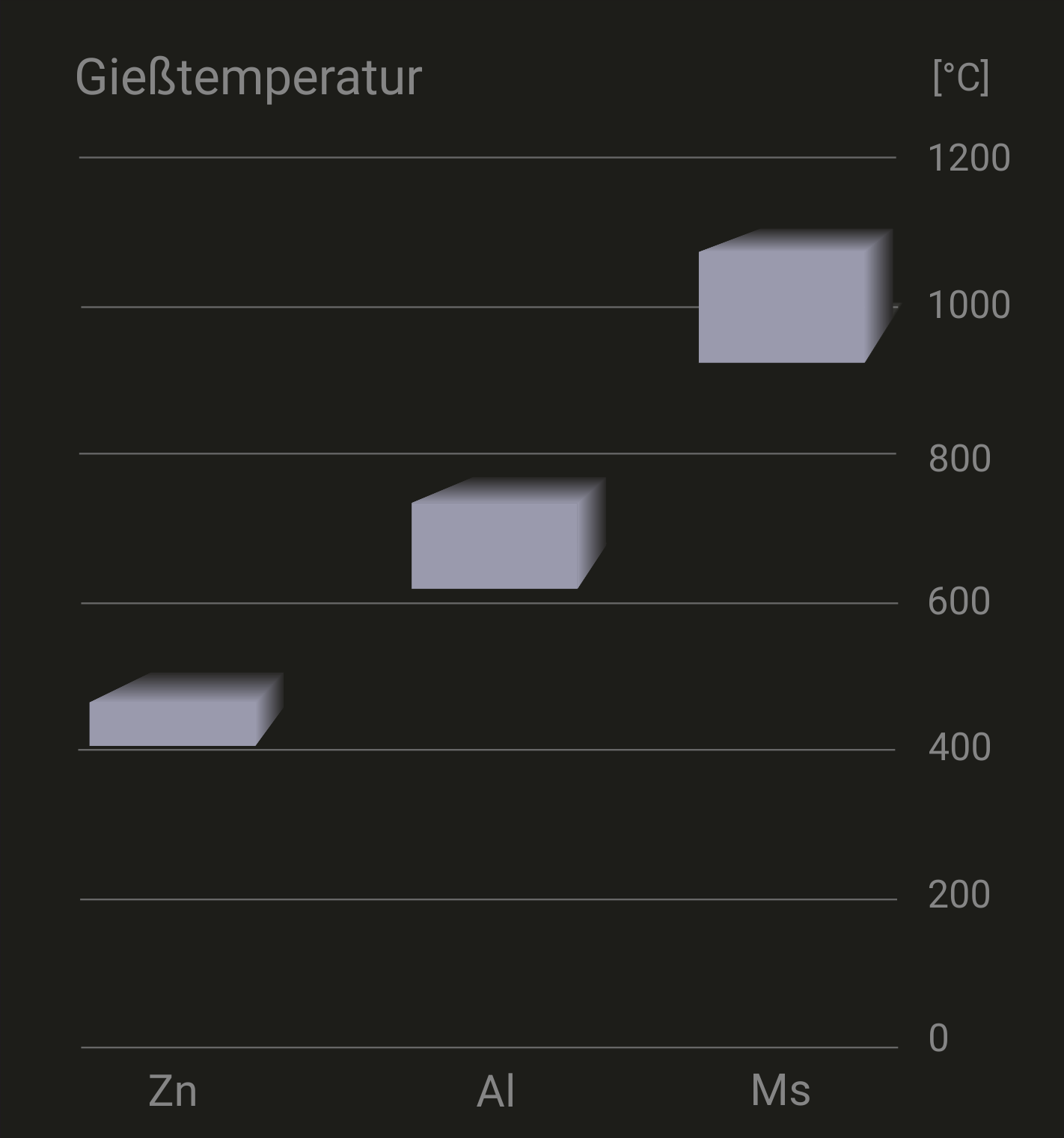
Gießtemperatur
Während die Gießtemperatur im Aluminiumdruckguss im Bereich von 640 – 710 °C und im Zinkdruckguss zwischen 410 – 430 °C liegt, lassen sich Messinglegierungen im Druckguss erst ab einem Temperaturintervall von 960 – 1050 °C vergießen. Das bedeutet zum einen, dass die Messinglegierungen bei sehr hohen Gießtemperaturen verarbeitet werden und so besondere Anforderungen an den Prozess stellen. Zum anderen hängt die Festigkeit bei Legierungen nicht selten von der Schmelztemperatur ab. Mit zunehmender Temperatur steigt in solchen Fällen die Festigkeit des Werkstoffs. Auch bei den im Druckguss verwendeten Messinglegierungen ist diese Analogie dementsprechend.
Warum erzählen wir Ihnen das?
Nur rein informativ, um Ihnen etwas mehr Hintergrundinformationen über das Verfahren zu geben. Denn die Beherrschung des Prozesses ist unsere Aufgabe. Für uns kein Problem, mit 65 Jahren Erfahrung im Messing-Druckguss, kennen wir jede Besonderheit.
Sie sehen, wir haben alles im Griff und so bleibt Ihnen mehr Zeit zusammen mit uns Ihr Projekt zu besprechen.
Festigkeit und Korrosionsbeständigkeit
Die Legierungen macht den Unterschied! Geht man von den erreichbaren Werten für die Zugfestigkeit aus, ohne Wärmebehandlungsmaßnahmen, so werden im Durchschnitt ca. 240 N/mm² bei gängigem Aluminium und ca. 300 N/mm² bei Zink erreicht. Im Vergleich dazu sind bei Messinglegierungen ohne Probleme Festigkeiten bis 350 N/mm² und bei Tombak bis 500 N/mm² erreichbar.
Es ist also möglich, die im Druckguss vorteilhaften dünnen Wandstärken des Bauteils mit gesteigerten Anforderungen an die Festigkeit zu kombinieren und schlussendlich zu realisieren. Gepaart mit der bereits erwähnten guten Korrosionsbeständigkeit von Messinglegierungen, bei Trink- und Brauchwässern, und einer sehr guten Beständigkeit gegenüber Salzwasser bei Tombak, beschränken sich die Einsatzgebiete dieser Legierungen nicht mehr nur auf den sanitären Sektor.
Vielmehr finden sich Druckgussteile aus Messinglegierungen in Offshore-Anlagen und im maritimen Sektor wieder, denn komplexe dünnwandige Bauteile, die ohne, meist aufwendige, Oberflächenveredelungen auskommen, führen zu enormen Einsparungspotenzialen.
Ist das nicht ein echter Gewinn?
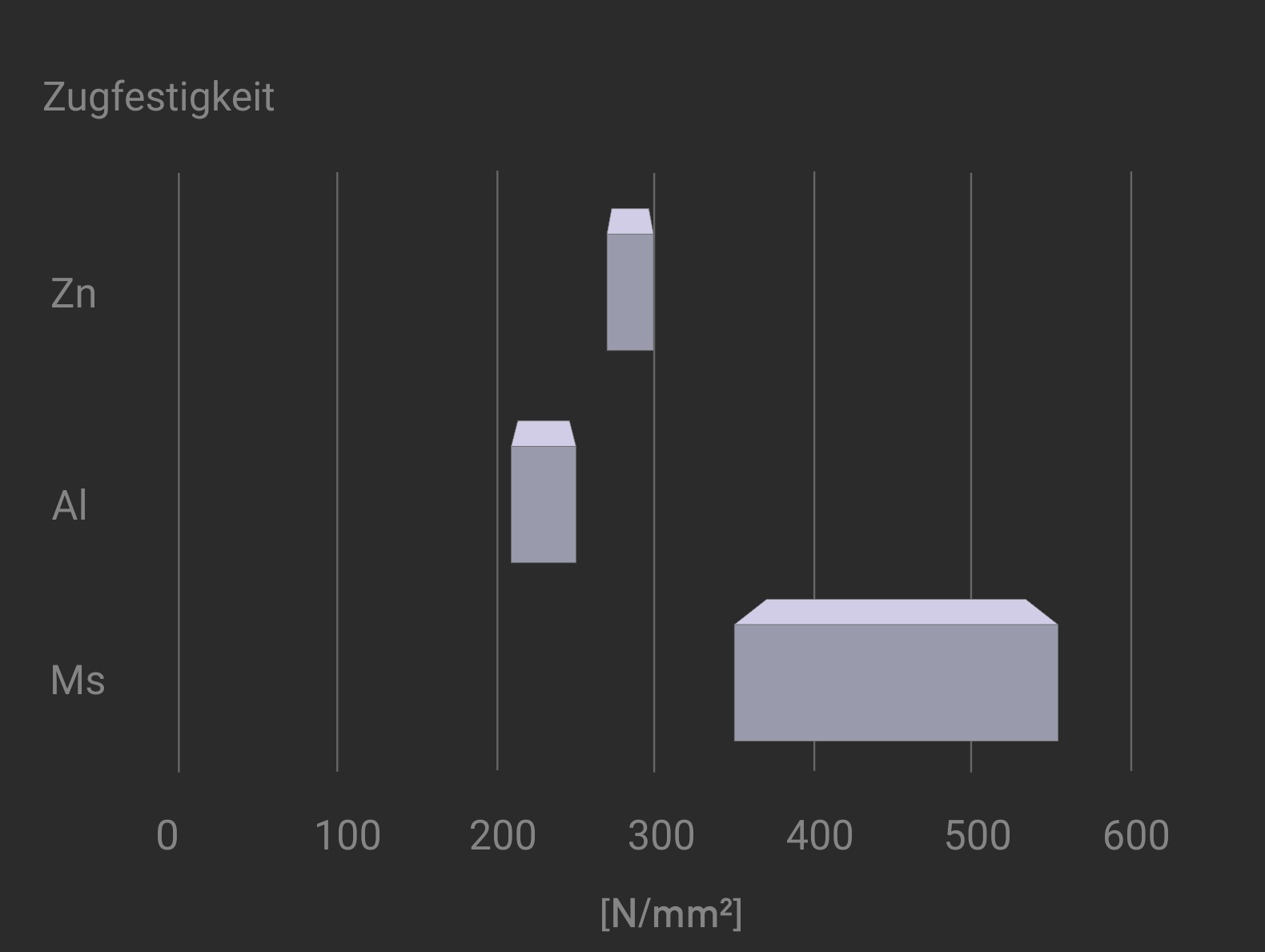
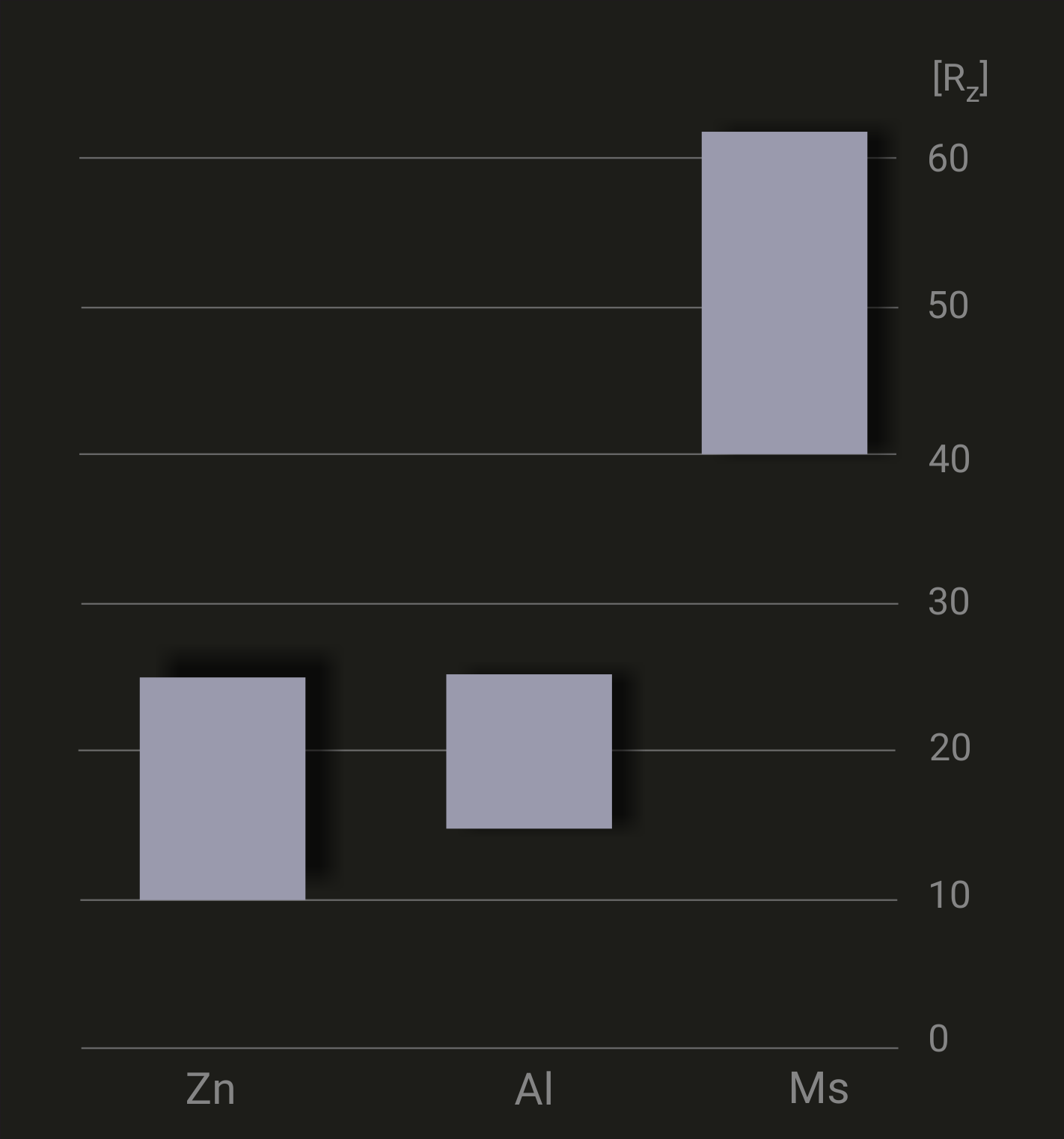
Oberflächenrauheit
Aufgrund der hohen Gießtemperaturen bei Messinglegierungen im Druckguss findet ein Verschleiß der Oberfläche der Formgravuren bereits früher statt als bei anderen Legierungen im Druckguss. Daraus resultiert eine Vergrößerung der Oberflächenrauheit, die im Bereich von Rz 40 – 63 μm liegt. Es gibt jedoch noch eine zweite Ursache für die erhöhte Rauheit:
Die Schmelze an sich erstarrt zu einem gröberen Gefüge als bei Aluminium- oder Zinklegierungen. Aber dennoch in einem feineren Gefüge im Vergleich zu anderen Gießverfahren wie z.B. Sandguss (Rz 100 – 150 μm).
Wenn die Wahl auf Messing-Druckguss fällt ist jedoch meistens die Oberfläche nicht das heikle Thema. Hier kommt es dann auf abbildungstreue Serienteile an, die möglichst endkonturnah gefertigt werden und ohne großen mechanischen Zerspanungs- oder Nacharbeitungsaufwand eingesetzt werden können.
Ein klarer Vorteil für Messing-Druckguss!